Research
Research for climate targets
Cutting-edge research is guaranteed by a world-class research team, international networking, multidisciplinarity and a unique large engine test bed infrastructure. The centre is one of the world’s three leading research institutions in the field of sustainable large engine development. Prof. Nicole Wermuth has been the scientific director of the centre since June 2024.
The LEC conducts research in five main research areas: Combustion & Fuels, Implementation, Engine Components and Sensorics, Integrated Systems und Simulation-based Development, which operates across domains. With the COMET Module LEC HybTec, the research focus became even stronger on the integration of big data methods in order to map phenomena that could not be modeled so far. Research in the COMET module LEC FFF will will provide the scientific basis for advancing the use of ammonia in combustion engines. Prof Nicole Wermuth is the Centre’s scientific director since June 2024.
All published research results from the LEC can be found on the webpage LEC Publications.
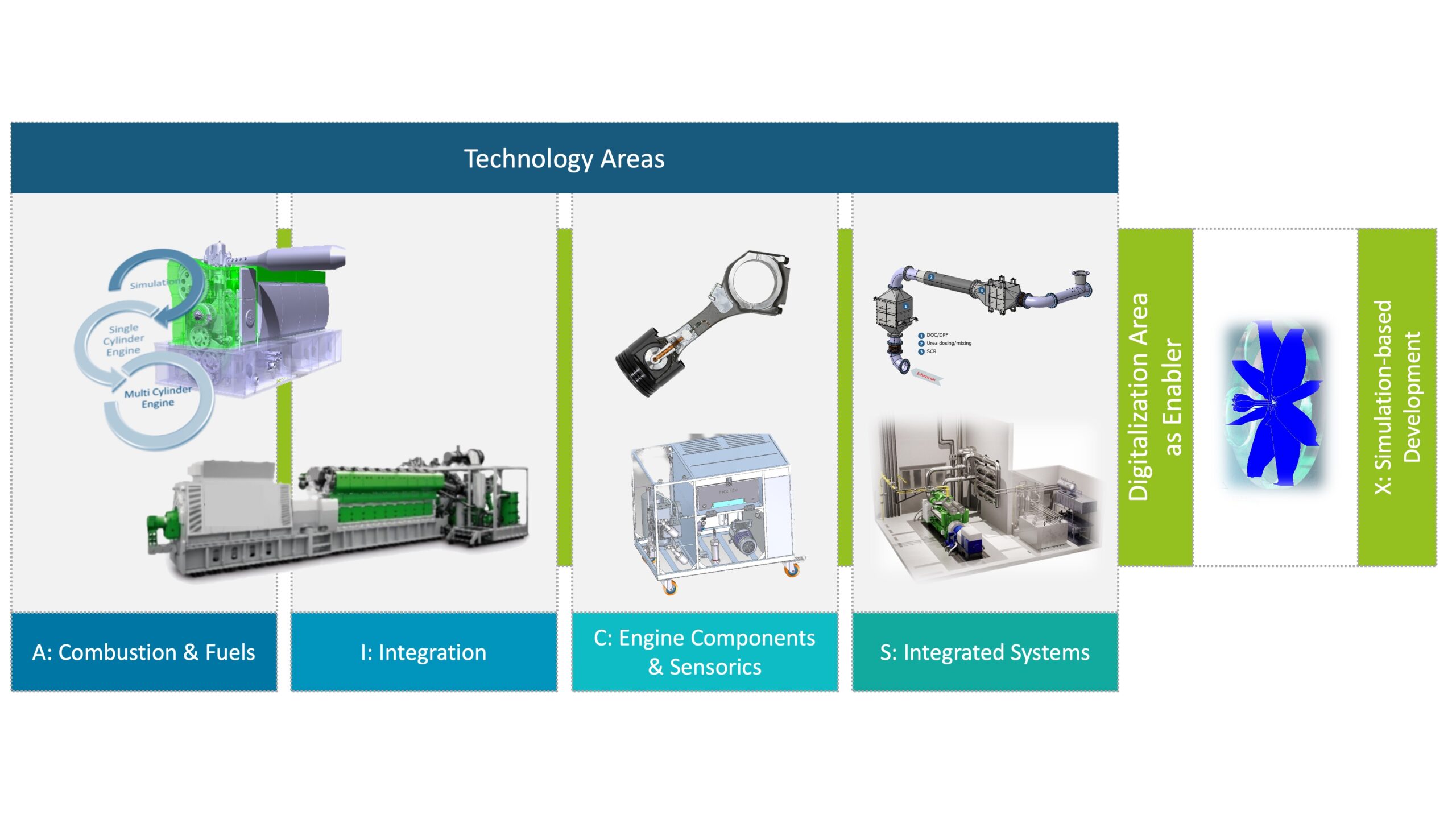
COMET RESEARCH AREAS
|
COMET MODULES
|
Combustion & Fuels
Area A
The area Combustion & Fuels area conducts applied research into the development of combustion processes and systems for green fuels such as hydrogen, ammonia and methanol, while at the same time demonstrating high overall efficiencies and power densities as well as minimising emissions.
- Engine concepts for renewable, electricity-based fuels
- Zero-impact emissions combustion concepts
- Fuel-flexible combustion systems and retrofit solutions
- System requirements and assessment of new technology concepts
The decarbonization of the world’s energy sectors also requires a fuel transformation for large engine applications in high-power systems. Use of net-zero carbon fuels while providing zero-impact emissions regarding climate change and air quality and still delivering high power density and high overall efficiency are the challenges that new and already existing energy and transportation systems are facing.
This research area aims to lay the scientific foundation for the development of combustion processes for green fuels such as hydrogen, ammonia, and methanol and to develop combustion systems for spark-ignition and compression ignition engine concepts. Experimental validation of new concepts, injection technologies and new actuators on single cylinder research engines and the transfer of these concepts to multicylinder engines are at the core of the research activities.
Area Manager: Dr. Maximilian Malin
Engine Components and Sensorics
Area C
The area Engine Components and Sensorics is entirely dedicated to engine reliability and durability, especially with regard to future fuels, and develops highly innovative monitoring instruments for engine components and lubricants.
- Monitoring and assessment of highly stressed engine components
- Development of specific sensor solutions and condition-based maintenance applications
- Experimental and simulation-based investigations on the tribological behavior of the core engine
- Expertise in terms of lubricant consumption measurement and chemical analysis of the interaction between oil, engine components, fuels and combustion concepts
Modern high-performance large engine systems for various applications must have a very high power density and be multi-fuel capable. However, these requirements bring challenges in terms of reliability, durability and maintenance costs. Increasing power output, which leads to very high peak pressures in the cylinders and high loads on the individual components, adds to the complexity. In addition, the use of new fuels may require optimization of existing components.
To this end, our interdisciplinary team contributes to solving these challenges by developing novel sensor solutions embedded in telemetry systems developed on demand, improving tribological simulations and experiments, and optimizing the lubrication situation for the challenges of using future fuels.
Area Manager: Dr. Michael Engelmayer
Integrated Systems
Area S
The area Integrated Systems is active in environmentally friendly system solutions for the energy and transportation sector based on the optimal integration of all subsystems into the respective overall systems, with a focus in the following fields:
- Catalyst technology and exhaust gas aftertreatment systems
- Carbon capture, storage and utilization technologies
- Techno-economic evaluation and optimization of overall systems
- Demonstration of sub-systems and overall systems on the engine system test bed
Establishing large engines as part of an ecologically sustainable energy transition requires innovative measures to minimize pollutant and greenhouse gas emissions. To meet the most stringent emission regulations, exhaust gas aftertreatment systems are optimized specifically for conventional and alternative fuels and integrated into the respective overall systems. Since carbon-based fuels will continue to be indispensable for many years, technologies for carbon capture and subsequent storage or utilization will play a decisive role in the future. The evaluation of the latest capture technologies depending on the application and the selection of the optimal technologies from a techno-economic point of view is carried out on the basis of system simulation-based investigations. The analysis and optimization of entire energy and transport systems (e.g., power plants, ships), considering the latest technological developments, provide the basis for selecting the optimal future technology paths for the specific applications. Finally, the testing of the developed sub-systems and overall systems as well as the demonstration of the transferability of the results to real systems are carried out at the new LEC multi cylinder system test bed.
Area Manager: Dr. Christoph Redtenbacher
Simulation-based Development
Area X
The Simulation-based DevelopmentArea is the ‘enabling area’ responsible for the models and methods at the LEC and provides suitable tools and models for research work in the technology-oriented areas across all domains.
- Development of numerical methods for the analysis and simulation of complex processes such as ignition, combustion and emission formation, taking into account the characteristics of renewable fuels
- Combination of physics-based and data-driven modeling approaches to increase the efficiency and accuracy of simulation and analysis methods
- Data-driven methods for condition monitoring and condition-based maintenance of large engines
- Comprehensive modeling and optimization of complex energy and transportation systems using multidisciplinary simulation and analysis methods with a focus on the integration of renewable energy sources
- Provision of tailor-made simulation tools to automate and accelerate the development process as well es ensure the transferability of results
The provision of scientifically sound fundamentals as well as the reliable simulation of highly complex processes are nowadays key for successful technological developments, especially with regard to the transformation to renewable fuels. To this end, detailed models and methods for the simulation of all subsystems as well as their interaction within the overall system are being elaborated. Relevant physical phenomena are investigated and supported by in-depth experimental work; stochastic processes are modeled by data-driven approaches. The data obtained through the increased integration of sensor technology in large engines is used with modern data-driven methods to enable targeted condition monitoring, condition-based maintenance and control of components, engines or complete systems. The knowledge gained from the comprehensive method development is incorporated into the LEC analysis and simulation methodology. In line with the strategy of increasing the overall share of simulation tasks in the development processes, the focus of the area Simulation-based Development is on establishing a simulation environment that enables reliable analysis and virtual development of all processes relevant to large engine applications.
Area Manager: Dr. Gerhard Pirker
LEC HybTec - HYBRID TECHNOLOGIES FOR ENHANCED RELIABILITY OF ULTRA HIGH-PERFORMANCE ENGINES
COMET Module (Project duration 2020-2023)
The COMET Module LEC HybTec combines complementary technologies to hybrid approaches in order to derive completely new concepts for the optimization of energy and transportation systems that meet the challenges of the future.
- Hybrid simulation methods for the prediction of stochastic phenomena in combustion engines
- Optimization of overall systems combining renewable energy sources, energy converters, novel energy carriers and energy storages
- Tribological simulation of the piston/ring/liner system to predict friction, wear and lube oil consumption.
- Improving the wear resistance of spark plug electrodes by coating them with novel hybrid metal-ceramic materials.
To enable sustainable solutions for highly flexible power generation and transportation systems, large engine technology must achieve reduced emissions while maintaining optimal performance parameters and increased robustness. Furthermore, all necessary components of the overall system as well as the interactions between these components must be optimized.
The hybrid approaches considered in the research program focus on combining physical and data-driven models to understand stochastic phenomena such as cycle-to-cycle variations or knocking in engines, to improve the prediction quality of the simulation, and to increase the quality of engine and combustion control as well as overall system performance, especially with respect to operation with CO2-neutral fuels. The use of ceramic-metal material combinations in the design of highly stressed engine components such as spark plugs extends the hybrid approach.
COMET Module Manager: Dr. Gerhard Pirker
LEC FFF - FUTURE FUEL FUNDAMENTALS
COMET Module (Project duration 2024-2027)
The COMET Module LEC FFF develops the scientific basis for new development methods and development tools to support the use of ammonia as a fuel in CO2-neutral energy and transportation systems.
- Basic experiments and analyses of ammonia spray formation, combustion and emissions
- Detailed modeling of ammonia spray, as well as ammonia/hydrogen combustion and emissions
- Long-term stability of lubricant and component materials in use with ammonia combustion
In contrast to hydrogen, ammonia can be transported and stored in liquid form at ambient temperature and only slightly increased pressure, which makes it particularly attractive for mobile applications such as locomotives, ships and mining vehicles as well as for seasonal energy storage. The differences to conventional fuels, especially in terms of combustion properties, emissions and the effects on the tribological system, require a significant revision of existing models and development methods.
The COMET Module LEC FFF comprises research work on the characterization of ammonia flames and the understanding of all relevant processes that take place in the ammonia injection and within the flame front. The detailed modeling of these phenomena is an essential building block for a predictive simulation methodology, as it is currently assumed that existing simulation models cannot be applied to ammonia combustion without significant adjustments or new developments. As part of the research work, the conversion processes of ammonia in injection chambers and combustion chambers are investigated experimentally, basic laboratory tests on the effects of the fuel and combustion products on lubricating oil and materials of engine components are carried out, and simulation models are improved and validated with the resulting measurement data.
COMET Module Manager: Dr. Gerhard Pirker